- Point of view
Manufacturing in 2024 and beyond: Experience at the heart of change
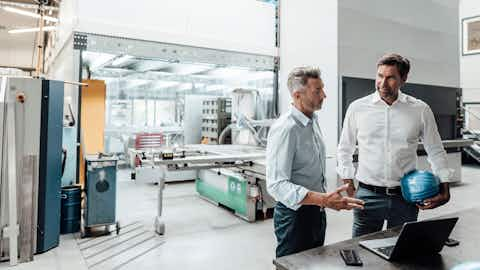
Improving digital maturity by balancing operational modernization and resilience
In 2023, manufacturing underwent a tectonic shift in how businesses navigated disruption. Amid ongoing supply chain challenges, automation and AI technology integration pushed companies toward smart manufacturing, improving efficiency and productivity across multiple sectors. Plus, sustainability grabbed attention, driving a surge in eco-friendly initiatives and greener processes.
With a renewed focus on achieving digital and analytics maturity for operational excellence and resilience in manufacturing, here are the top five trends to look out for in 2024.
1. Role-based upskilling programs fight skills gaps and workforce challenges
One of the biggest challenges for the manufacturing industry in 2024 will be the skills gap. A study by Deloitte and the Manufacturing Institute forecasts that US manufacturing will have 2.1 million unfilled jobs by 2030.1 So how do you tackle this problem to attract and retain the next generation of talent?
Plug the skills gap with role-based training and upskilling programs. Companies will continue to invest in automation and robotics to empower the workforce – making the industry more appealing to millennials and Gen Zers. Collaboration with educational institutions and vocational training centers will also play a crucial role.
Bridge skills gaps by:
- Training your teams to think lean processes to foster a culture of reducing waste and optimizing workflows
- Offering process knowledge management services to transition between a retiring and fresh workforce seamlessly
- Documenting workflows to standardize operations
- Creating virtual reality programs and supporting technician training to improve the speed to outcomes
2. AI and generative AI (gen AI) pave the way for smarter operations
There will be a higher appetite in 2024 for data-driven insights to deliver state-of-the-art target operating models. A recent McKinsey Global Survey reports that 40% of participating organizations will increase their AI investment because of advances in generative AI.2 Manufacturers will continue to make data analytics and AI investments into processes and systems for more accurate scenario planning, quality control, predictive maintenance, and risk reduction.
Manufacturers must increase digital maturity. This includes investing in IoT devices to gather real-time data, implementing AI and machine learning for predictive analytics, and adopting automation for repetitive tasks to gain a competitive edge.
Build efficient operations by:
- Implementing holistic solutions with a robust data and analytics foundation
- Designing a lean digital core that runs on integrated, cloud-based applications
- Advocating for responsible AI frameworks to drive explainable and ethical AI use for high-trust, bias-free governance
- Working with industry-specific implementation partners for infrastructure evaluation, reporting, end-to-end process visualization, and encouraging gen AI adoption to identify new ways of working
3. Supply chains become autonomous and networked for sustainable growth and resilience
Manufacturing supply chain leaders now have a seat at the strategies table. As reported by KPMG, more than six in ten global organizations expect geopolitical instability to impact supply chains in the next three years.3 Often, maintaining product quality while tracking regulations and scrambling for supplier/dealer visibility and real-time inventory planning can make scaling difficult, especially for complex product portfolios with longer production cycles. But there are ways to respond to these challenges.
Manufacturers must embed autonomous, networked supply chains into their business models. This will deliver better supply chain visibility and more control over market volatility, encouraging agile methods of working with less human intervention.
Pave inroads to resilient supply chains by:
- Embedding enterprise business planning to converge planning efforts across departments
- Harnessing collective AI capabilities, services, data, and knowledge across broader ecosystems
- Boosting supply chain technology ROI to elevate supply chain performance
- Using digital twins – virtual replicas of physical machines – to simulate and test machinery in a digital space
- Creating circular supply chain operations to cut down delays and improve time to value
4. Aftermarket services transformation wins customer loyalty
With changes in demand, market maturity, equipment sales, and pricing pressures, customers gravitate towards businesses that can support them throughout the purchase life cycle of products. How? Enter aftermarket services. The aftermarket services market size is forecasted to reach a value of $122.8 million in 2027 – a potential source of operational cash flow for organizations.4
Transform aftermarket services by collaborating with partners who bring industry knowledge and technology maturity to embed best practices into teams and operations. Your partners should share your goals and visions, evaluate risks, and value speed to innovation.
Wow customers with superior aftermarket services by:
- Implementing a connected dealer solution to optimize spare parts planning, resolve process complexity, and boost supplier visibility
- Using AI capabilities in remote monitoring and diagnostics to detect asset problems faster and reduce downtime
- Engaging a partner with proven credentials in transforming aftermarket operations
- Integrating aftermarket services into sales contracts to breed customer trust
5. Environmental, social, and governance (ESG) goals demand transparency
Sustainability is no longer a buzzword. Yet, 75% of manufacturers lack confidence in their partners' and suppliers' ability to support their ESG/sustainability goals.5 One of the main reasons is the need for more clarity on ESG goals.
Manufacturers must collaborate across the value chain to identify everyday operations where ESG strategies will add meaning. It's crucial to develop frameworks that provide visibility into company activities, assess outcomes, quantify carbon footprint, and develop ownership-based change management to support ESG initiatives and track progress.
Make your ESG strategy value-driven by:
- Defining purpose and success metrics to encourage stakeholder buy-ins
- Identifying and reducing carbon hotspots by embedding carbon data into processes and aligning with regulations, such as the European Union's Carbon Border Adjustment Mechanism (CBAM)
- Increasing resilience with circular operations through refurbishment, material security, and shorter supply chains to help respond to regulations like the Right to Repair and EU's Product Passport
- Improving fair operations by expanding decision criteria and considering the people and communities impacted in the value chain
The way forward: customer experience to go into overdrive
The speed with which the manufacturing landscape is evolving is remarkable. Experience is at the center of it all and will continue to drive manufacturers to position themselves for success. The urgency will kick off company-wide actions to address skills gaps, embrace technology, optimize supply chains, enhance aftermarket experiences, and prioritize sustainability. It's a journey that requires adaptability, innovation, and a commitment to reimagining a future fit for the next generation of manufacturers and their customers.
Shellie Molina, senior client partner, manufacturing, authored this POV | Follow her on LinkedIn
Sources
1. Paul Wellener et al., "Creating pathways for tomorrow's workforce today," Deloitte, May 4, 2021.
2. Michael Chui et al., "The state of AI in 2023: Generative AI's breakout year," McKinsey Global Survey, August 1, 2023.
3. "The supply chain trends sharking up 2023," KPMG, December 2022.
4. "Industrial Machinery Repair/Aftermarket Services Market Size, Share, Statistics, Trend Analysis and Forecast Report, 2020 - 2027," Market Decipher, September 19, 2020.
5. "Suppliers Are The Secret Sauce To Manufacturers' ESG Success," Forbes, March 29, 2023.